Understanding Precision Machining CNC
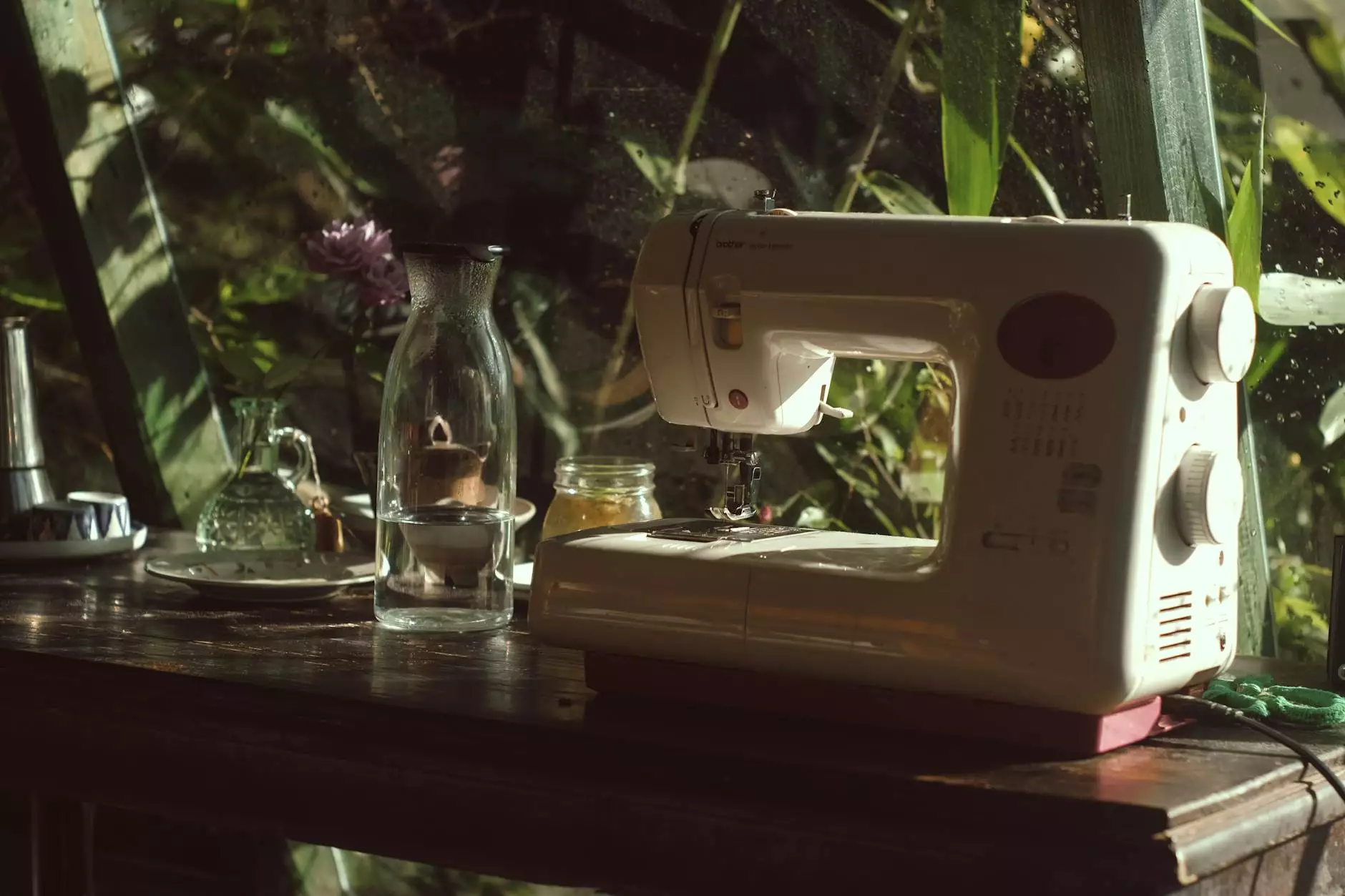
In today’s competitive landscape, businesses increasingly rely on advanced manufacturing techniques to deliver high-quality products. Precision machining CNC (Computer Numerical Control) has emerged as a pivotal process in the field of metal fabricators, revolutionizing how components are designed and produced. In this comprehensive article, we will explore the intricate details of precision machining CNC, its benefits, applications, and its crucial role in enhancing efficiency and accuracy in manufacturing.
What is Precision Machining CNC?
Precision machining CNC refers to a highly automated manufacturing process in which computer-controlled machines are used to remove material from a workpiece to produce parts to meet extremely tight tolerances. This technique allows for the creation of complex shapes and geometries that would be nearly impossible to achieve with traditional machining methods.
There are several key components to CNC machining, including:
- The CNC Machine: The core of the operation, which can include mills, lathes, routers, and grinders.
- Control Software: Programs that translate designs from CAD (Computer-Aided Design) software into machine language.
- Workholding Devices: Equipment that secures the workpiece during the machining process.
- Cutting Tools: Tools that remove material from the workpiece to achieve the desired shape and finish.
Benefits of Precision Machining CNC
Utilizing precision machining CNC technology offers several advantages that make it a preferred choice for many manufacturers.
1. Increased Precision and Accuracy
CNC machines operate with incredible precision. They can create intricate components that are uniform in size and shape, ensuring high-quality standards consistent with engineering specifications. This precision reduces the margin of error, enhancing both functionality and performance.
2. Enhanced Production Efficiency
CNC machining allows for rapid production cycles. Once a program is written and components are set, machines can operate continuously, processing large volumes of material without significant downtime. This efficiency is essential for meeting market demands quickly and effectively.
3. Flexibility in Design
Precision machining CNC is not limited to a single design or type of material. With the capability to easily switch between different programs, manufacturers can produce a variety of parts from different metals, plastics, and composites, making it ideal for custom jobs and rapid prototyping.
4. Cost-effectiveness
While the initial investment for CNC machining equipment might be significant, the long-term savings are considerable. The ability to produce parts faster and with fewer errors reduces labor costs and material waste, leading to overall lower production expenses.
5. Safety Improvements
CNC machines are designed with safety features that protect operators. Reduced manual handling of dangerous tools and materials minimizes the risk of accidents, ensuring a safer working environment.
Key Applications of Precision Machining CNC
The versatility of precision machining CNC technology allows it to be applied across various industries. Here are some common applications:
1. Aerospace Industry
The aerospace industry demands parts that meet rigorous safety and performance standards. CNC machining is used to create components such as engine parts, brackets, and housings that require exceptional precision and reliability.
2. Automotive Manufacturing
CNC machines play a crucial role in automotive manufacturing, producing everything from intricate engine components to body panels. The ability to machine complex features ensures that parts fit perfectly, enhancing the performance of the entire vehicle.
3. Medical Devices
The medical field often requires precision components that adhere to strict quality standards. CNC machining is utilized to manufacture surgical instruments, implants, and prosthetics, where precision is vital for patient safety and effectiveness.
4. Electronics Manufacturing
With the rapid advancement in technology, electronics manufacturing has seen a shift towards more compact and intricate designs. CNC machining is used to create cases, connectors, and circuit boards that are integral to modern devices.
5. Tooling and Die Making
CNC machining is essential for creating tooling and dies used in mass production processes. The accuracy of CNC technology ensures that these tools produce consistent and high-quality results over time.
The CNC Machining Process: A Step-by-Step Overview
To better understand how precision machining CNC operates, let’s walk through the typical steps involved in the CNC machining process:
Step 1: Designing the Part
The process begins with the design of the part using CAD software. Engineers and designers create detailed drawings that outline all specifications, dimensions, and tolerances.
Step 2: Converting the Design into G-code
Once the design is complete, it is converted into G-code, the language that CNC machines understand. This code dictates the movements of the machine, tool speeds, and feed rates.
Step 3: Setting Up the CNC Machine
Before machining can commence, the CNC machine must be set up. This includes securing the workpiece and loading the appropriate cutting tools based on the specific requirements of the job.
Step 4: Machining the Part
With the machine set up, the CNC machining process can begin. The machine executes the G-code instructions with precision, cutting away excess material from the workpiece to produce the final shape.
Step 5: Quality Control Checks
After machining, the finished parts undergo inspection to ensure they meet the required specifications. Quality control ensures each component performs as intended and adheres to industry standards.
Step 6: Finishing Processes
If necessary, additional finishing processes may be applied, such as polishing, anodizing, or coating, to enhance the part’s appearance and corrosion resistance.
Challenges in Precision Machining CNC
While precision machining CNC has many advantages, it is not without its challenges. Manufacturers must navigate various issues to ensure optimal performance.
1. High Initial Investment
The initial cost of CNC machines and the software required can be substantial, posing a barrier for smaller businesses. However, the long-term benefits often outweigh these initial expenses.
2. Skill Requirements
Operating CNC machinery requires skilled technicians who are trained in both programming and machine operation. Ongoing training is essential to maintain expertise and keep up with technological advancements.
3. Maintenance Needs
CNC machines require regular maintenance to ensure they operate efficiently. Downtime due to maintenance can result in delays in production schedules.
4. Material Limitations
Certain materials can be challenging to machine using CNC technology. Manufacturers must select appropriate materials and cutting tools to prevent issues such as tool wear or breakage.
The Future of Precision Machining CNC
The future of precision machining CNC appears bright as technology continues to evolve. Some emerging trends include:
1. Greater Automation
Advancements in automation technologies, including robotics, are expected to streamline the CNC machining process further. This evolution will enhance efficiency and reduce reliance on skilled labor for routine tasks.
2. Integration with Additive Manufacturing
As 3D printing technology matures, integrating CNC machining with additive manufacturing principles is likely to produce hybrid systems capable of both subtractive and additive processes. This convergence could revolutionize component manufacturing.
3. Enhanced Software Solutions
Developments in software solutions will allow for better simulation and predictive capabilities, enabling manufacturers to optimize their machining processes and reduce errors before actual machining occurs.
4. Sustainable Practices
With growing emphasis on sustainability, the CNC machining sector is exploring ways to minimize waste, reduce energy consumption, and select eco-friendly materials, aligning with global sustainability efforts.
Conclusion
Precision machining CNC stands as a cornerstone of modern manufacturing, enabling businesses to create components with unmatched precision and efficiency. As the industry continues to evolve, this technology will undoubtedly play an even more significant role in shaping the future of manufacturing. At DeepMould.net, we embrace the cutting-edge capabilities that CNC machining brings to the table, allowing us to provide superior solutions tailored to our clients’ needs. By understanding and leveraging the advantages of precision machining, metal fabricators can meet the demands of various industries and uphold the quality standards necessary for success.
For any inquiries about our CNC machining services and to discover how we can help you with your custom metal fabrication needs, visit us at DeepMould.net.